Warehouse Management System - WMS
Optimizes the organization of warehouse flows, from receipt of goods from the production department (or from supplier purchases) up to shipping and management of returns. Allows for tracking of the position of all load units.
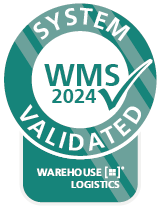
Fraunhofer IML validation
In 2024 Onit reobtained the Fraunhofer IML validation for On.Plant/WMS.
The important German research institute, part of the largest applied research organization in Europe (Fraunhofer-Gesellschaft), has certified the quality of the software which allows for optimal organization and complete tracking of warehouse flows, from receipt of goods to shipping and returns management.
Description
Thanks to an innovative direction, the WMS allows you to supervise all warehouse operations and to distribute workloads based on roles and work areas.
The operators are guided in the phases of goods receipt, storage and shipment preparation, interacting with the system through the operating devices commonly used in warehouses.
The flexibility of the software allows for integration with the company ERP and with various automatic systems.

Advantages
- Reduction of stock in the warehouse thanks to the monitoring of stock and stock outages
- Reduction of the cycle time of warehouse activities
- Reduction of FTE (Full Time Equivalent) thanks to optimization of storage locations and scheduling of missions
- Improvement of the quality of shipments, with fewer errors and fewer delays
- Reduction of inventory adjustments thanks to the algorithm for the correct cyclicality of product stock
- Increase in supplier quality control (incorrect palletization, labeling anomalies, shelf life, delays, etc.)
WMS features that improve your work
Goods inflow
Identification and counting of the incoming product from supplier and production. Labeling and quality controls, with the possibility of customizing the characteristics of the product that will be visible in stock.
Put-away
The software proposes to the warehouse operator the best location based on the characteristics of the product, its movement rates and the physical characteristics of the warehouse. Certification of the actual position of the stored product. Cross-docking.
Stock
Stock is aligned in real time with warehouse operations. It is possible to view the individual loading units or group by desired product features. Customizable management of the product features to be assigned to the stock.
Transfers
In Multi-Plant installations, this module allows to organize transfers between the different sites, using all the mechanisms of outbound and inbound features, avoiding product re-labeling and ensuring control of the operational flow.
Procurement
If logistics also services a production department, the transfers necessary to guarantee production continuity are automatically generated. Supply buffers that follow production speed, guaranteeing the right stock.
Replenishment
Automatic generation of replenishment requests from the Stock area to the Picking locations, configurable on the basis of thresholds or order analysis (deliveries, transfers, production requests). Distribution of the workload of forklift drivers according to area or aisle.
Handling of full pallets
Each operational flow (Incoming goods, Shipping, etc.) can generate movements managed by an integrated system which, based on the roles of competence, optimizes the assignment of activities to operational resources, balancing workloads and optimizing the process.
Picking
The flow of picking can be configured according to the working methods (Single Order, Multi Order, Batch & Sorting, Zone Picking, Pick&Pack), selecting between picking scenarios of Man-to-Goods (operator in motion) or Goods-to-Man (goods in motion).
Outgoing goods
The progress of the preparation flow is updated in real-time and is visible by all company roles. The vehicle loading flow is managed in its entirety: from checking the driver/vehicle upon entry, to checking the weight upon exit, through the verification of the products loaded into the truck.
Inventory
- Inventory planning by area, racks, articles, articles' attributes
- Cycle or event-based inventory (e.g. articles with picking movements)
- Inventoried or to be inventoried Handling Unit registration
- Inventory report
Operational devices
Each operational phase is combined with the use of suitable devices to optimize usability (Android rugged devices, Pick-to-Light, Vehicle mount computers, etc.). There are multiple options to select: from Onit's wide-range of certified devices, to the certification of different hardware already used in your company.
Automation
Storage and picking execution are highly automatable activities. The WMS has several Standard APIs with which it is possible to interact with external systems or, if necessary, it can be adapted to complex integrated automation projects.
Logistics costs
Possibility to select different types of price lists, configurable for each owner of the goods on the operational flows (entry, exit, stock, etc.). For subcontractors, the module provides a billing proposal to customers. For NON subcontractors, an indication of the logistics costs.
KPIs Report
Each operation within the WMS is logged with user and resource definition, creating a database for standard reports on the productivity of the various phases. It is also possible to obtain customized reports.