Manufacturing Execution System - MES
Coordinates all production activities, collects data from the machines and allows for their real-time monitoring. It allows for the management of the consumption of raw materials and the labeling of the finished product, detects and classifies production downtime and labour.
Description
The production management module allows for simple and intuitive monitoring of all the stages of the production process, combining order data with the parameters obtained from the production lines, thus allowing for continuous and effective monitoring of the finished product quality.
The classification of downtime and labor management allow the module to manage and control the production lines correctly.
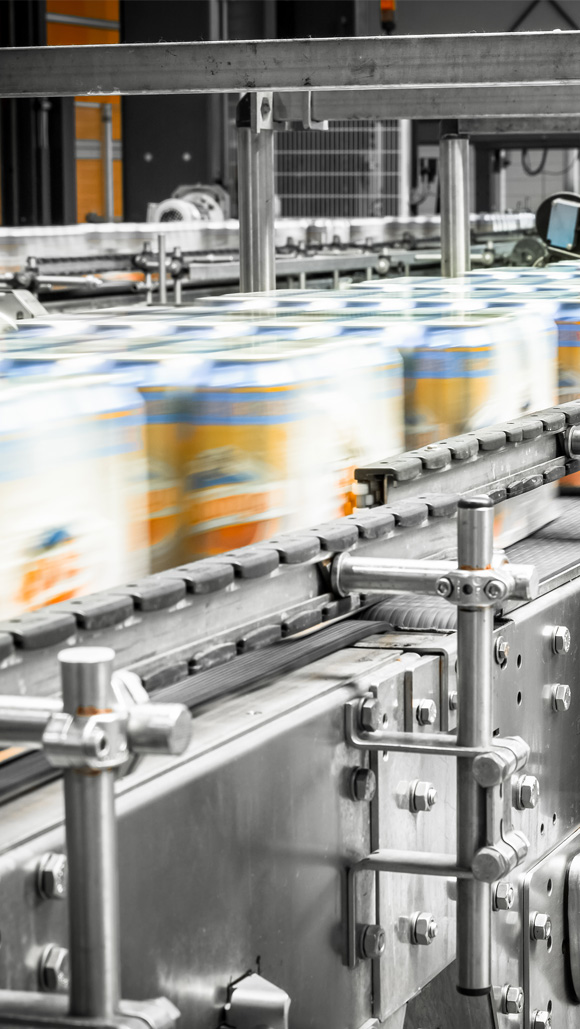
Advantages
- Continuous monitoring in the department and in the control room
- Link between production planning and execution
- Timely cost allocation for accurate accounting
- Search by product tracking and traceability
- Elimination of non-value added management activities and record storage
- Collection of quality and productivity data for business improvements
MES features that improve your work
Bills of Materials
Management of bills of materials and their variants, management of replacement items for components and waste items for production. Possibility to customize the production parameters based on the production line.
Work Orders
Scheduling of work orders on the production lines of the various departments, possibility of dividing the different types of processing by organizing the production plan and sequencing the work orders.
Line Monitor
All functions for work order monitoring and management available to operators. Definition of consumption, product labeling, verification of supply and available stock to avoid production interruptions due to lack of product.
Labor
Identification of the workforce, definition of roles and type of activity. The system adapts to the type of processing by recording both the final workforce and the current one, through identification of staff.
Machine downtime
Recording of production stops on the lines. The stop can be entered manually by the operators or detected automatically through machine interfacing and subsequently sorted by its cause. Identification and monitoring of production yield.
Productive Targets
Possibility to define productivity goals per item (or family) basis (e.g. line speed, waste, unscheduled stops), real-time monitoring of goal achievement progress and comparison with trends and budget.
Operating Instructions
Possibility to define the operating instructions to follow a correct setup or closure of the plants, on the work orders. The instructions can also be declared mandatory in order to proceed with production, linking the result to the activation of the machines.
Integration and Automation
Integration with field devices (scales, dispensers, printers, etc.) and automation systems (AGVs, Palletizers, etc.) to automate operations as much as possible, reduce the number of declarations required from operators and therefore the probability of human error.
Reports and KPIs
Various reports allow the supervisor to analyze the data collected during the various stages of production. With Business Intelligence tools it is possible to customize views and analysis dimensions.
Tracking
The system includes various utilities to obtain product tracking reports, both "downstream" and "upstream". Each single Unit of Load (UoL) is tracked in its use and allows the production lot to be monitored in all its phases.