The secret to the perfect pizza? Perfect logistics too.
The On.Plant/TMS system has provided Roncadin with advanced features that have enabled it to optimize the management of its shipments.
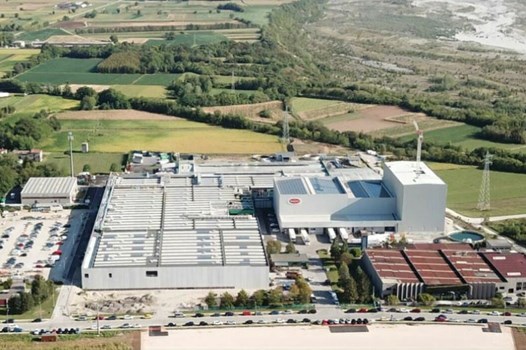
Roncadin SpA SB
Based in Meduno (Pordenone), the company was founded in 1992 to produce high-quality Italian pizza for large-scale national and international distribution. Today, the company employs around 850 people, with a turnover in 2024 exceeding €200 million and producing around 100 million items per year.
Pizzas and snacks are made with the highest quality ingredients and a production method that reproduces the characteristics of traditional pizza, including baking in a wood-fired stone oven and hand-topping.
Since 2021, Roncadin has been a Benefit Corporation, committed to operating responsibly towards the environment, people, and the local area, with a view to sustainable development.
Roncadin's mission is to bring the authentic taste of Italian pizza to homes around the world, combining traditional craftsmanship and technological innovation.
200
million in turnover
850
employees
100
million pizzas per year
Customer needs
The former TMS used by Roncadin was no longer able to adapt to the company's growing needs, linked to the increase in loads and the need to plan shipments not only from the head office but also from external logistics, while keeping transport costs under control.As the market extends overseas, shipments are made by both road and container, a situation that involves a high degree of load heterogeneity that is not always easy to manage. This heterogeneity makes load preparation difficult to plan, a situation that leads to high congestion in loading bays.
The company therefore decided to adopt new software for shipment planning and costing: a tool that would allow it to manage every aspect of transport strategically: Onit's On.Plant/TMS was able to meet all these needs.
On.Plant solution
Following an intense and thorough testing and trial phase, Onit launched On.Plant/TMS and completely replaced the old software, also expanding the available features, ensuring the longevity of the system, and allowing it to be easily evolved to adapt to the company's development.
All shipment management, from planning to cost verification, has been digitized and made simpler, faster, more efficient, and more accurate.
On.Plant/TMS has thus enabled Roncadin to plan all shipments in Italy and abroad and to calculate transport costs for each trip in real time, integrating with the company's management system and thus allowing for prudent choices in terms of economic savings.
In addition, through the Slot Booking module, Roncadin operators can book the time at which to carry out loading/unloading operations, a task made easier thanks to the software's suggestions on available and bookable time slots.
The extension of the project then led to the activation of the YMS (Yard Management System) module, which made it possible to manage the entry/exit of vehicles in the depot in an orderly and efficient manner. The software provides a list of all expected vehicles, each with its own booked time slot and details of the movements it must perform.
With the aim of streamlining the work of the gatehouse staff by automating acceptance operations, an interactive totem was also installed at a later stage to allow drivers to directly enter the data required for acceptance and scan the documents requested upon arrival. When called to the bay, the driver receives an SMS on their cell phone indicating the loading/unloading bay where they must report.
Achievements
The On.Plant/TMS system has provided Roncadin with advanced planning, time slot booking, and driver arrival management capabilities, enabling it to optimize the management of its shipments, reducing costs and increasing efficiency.
The scheduling of shipments, both by truck and container, is now optimized, and the loading and unloading bays have an organized, congestion-free workflow. A feature has also been activated that allows for accurate counting of pallets from incoming and outgoing loads, simplifying the procedures for keeping track of them.
Furthermore, thanks to integration with existing information systems and the autonomous driver check-in system based on totems, Roncadin has achieved greater simplification of procedures and better experience for its customers and suppliers.
1.000
trips per month planned
70
carriers
20
planners/warehouse workers