Fanatics streamlines merchandise and order management
Fanatics can now count on a well-organized warehouse and a set of tools that simplify the product customization process.
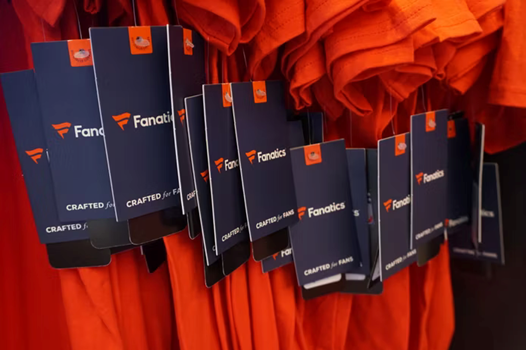
The client
When it comes to sports merchandise, it's Fanatics
Fanatics is an American multinational company, a leader in sports merchandising, with annual revenues of several billion dollars.
In 2023 Fanatics acquires EPI: an Italian company based in Milan that manages retail and merchandising activities on behalf of several Italian soccer and basketball league teams.
EPI thus becomes Fanatics Italy, a leading reality in the sale of official and personalized sports merchandising relying on three warehouses: one in Segrate (MI), dedicated to physical stores and ecommerce, one in Turin and one 3PL, the latter organized to supply several physical stores.
https://www.fanaticsinc.com/epi
3
warehouses
1,000
shipments/day
Customer Need
The warehouse becomes strategic
With the acquisition of EPI by Fanatics, the Segrate warehouse was identified as a strategic element and it was therefore decided to equip it with an MES and WMS system, absent until then, so as to digitize and optimize the processes of goods management and order fulfillment.
On.Plant Solution
MES and WMS to manage warehouse, customizations and shipments
An average of about 1,000 shipments/day are made from the Segrate warehouse, manned by warehouse managers, workers and those responsible for customizing the teams' competition kits. Many of these shipments involve customized products, i.e., base shirts to which numbers, letters and patches are applied: this is a real “production” and as such must be managed with MES software.
As a result of Onit's intervention, the planning of production orders (so-called “customizations”) through On.Plant/MES is done by managing the theoretical loads/unloads of all components (e.g., letters, patches, etc.) except for the main component, i.e., the T-shirt-base.
The business intelligence capabilities of On.Plant/WMS, moreover, have enabled Fanatics Italia to simplify procurement management and avoid running out of items needed for production.
Achievements
Leaner processes, fewer errors, precise traceability and greater adaptability
Thanks to On.Plant/WMS and On.Plant/MES, Fanatics Italy can now count on a well-organized warehouse and a number of tools that simplify the product customization process, bringing with them these benefits:
- Increased operational efficiency
-
- Reduced operational time: thanks to the optimization of the User Experience, the process has gone from 15 to 3 clicks, speeding up the execution of customization orders
- Scheduling Automation: theoretical loads/unloads of components are automatically managed, reducing manual work
- Cost reduction
-
- Less errors and waste: digital management of production and logistics processes reduces errors in customizations and shipments
- Supply optimization: the risk of production downtime due to lack of materials is avoided
- Improved control and traceability
-
- Real-time monitoring: MES provides up-to-date data on processing status and material consumption
- Data analysis: business intelligence features enable analysis of warehouse and production process performance to identify further room for improvement
- Greater flexibility and adaptability
-
- Effective customization management: MES system allows large-scale custom orders to be planned and managed without compromising productivity
- Scalability: the process is ready to handle larger volumes of orders without proportionally increasing operating costs
- Sustainability and resource optimization
-
- Less waste: more precise supply management reduces material waste
- Less energy consumption: faster, automated processes require fewer resources