Optimizing ceramic warehouse logistics with WMS software
Integration of WMS management software in the ceramics industry: from inventories to shipments and returns.
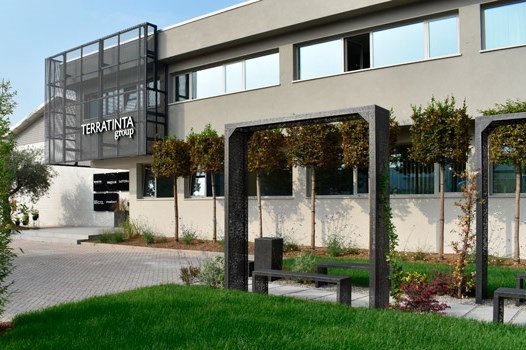
A Supplier and wholesaler of ceramics active worldwide
Terratinta is a company active in the ceramics industry. They are engaged in the production of ceramic and porcelain tiles for indoor and outdoor spaces, and public and private architectural projects. They are leaders in the production of floor and wall tile finishes with a North European design and are involved in all-around supplies, marketing a wide range of products with different styles and designs.
The company is one of the ceramics wholesalers whose four brands cover more than 50 countries worldwide.
35
employees
25 million
turnover
B Corp
certification
Client's need
Innovation and evolution: a new WMS software
Terratinta presented the need to innovate processes related to the organization of inventories with a new complete and efficient WMS management software, and to introduce a protocol of guided procedures for operators during the acceptance and preparation of goods. This need stemmed from the company's desire to evolve technologically, following the "use less paper " philosophy dictated by the sustainability policies that later led to B Corp certification: operators were dealing with warehouse management procedures exclusively in manual mode and with only paper support. In response to Terratinta's needs, Onit analyzed the situation and provided the company with specific advice on optimizing warehouse flows.
This led to suggesting to Terratinta, as a solution, the integration and implementation of On.Plant's WMS - Warehouse Management System software. The project was approved with great enthusiasm by the company and was included as a goal to commission the software at the new logistics facility that was being activated.
On.Plant's Solution
WMS: a ready-to-use integrated solution
The proposal put forward by Onit to meet Terratinta's needs focused mainly on the integration of the WMS solution.
Leveraging its strong experience in the ceramics industry, gained over many years of logistics projects, Onit integrated the On.Plant/WMS software with Terratinta's systems to optimize the organization of warehouse flows, from the receipt of goods from the production department to shipping, inventory management and returns. The WMS management software enables to supervise all operations taking place in the warehouse and to distribute assignments according to roles and work zones.
In addition, the WMS provides several features that can facilitate and improve management in the warehouse:
- Incoming goods: identify and count incoming goods from suppliers and production;
- Transfers: organization of transfers between different company facilities, taking advantage of goods entry and shipment flow mechanisms;
- Picking: flow of picking that can be configured according to work modes;
- Inventory: real-time alignment of inventories with warehouse operations;
- Procurement: automatic generation of transfers in the case of continuous servicing of a production department;
- Automation: storage and picking are automatable;
- Operating devices: useful devices to improve usability at each operational stage;
- Logistics costs: selection of different types of price lists that can be configured for each owner of inventory on operational flows;
- Inventory: inventory planning by area, shelf, item and item attributes;
- Goods exit: visualization of goods preparation flow in real-time and searchable internally within the warehouse;
- Whole pallet handling: integrated instructions(?) in the warehouse that oversee the assignment of tasks to operational resources based on workloads;
- Lowering: automatic production of requests to lower stock locations to picking locations;
- Put-away: visualization of the best location of goods at the time of storage based on product characteristics.
Four months after the start of the collaboration with Terratinta, the WMS software was already active in the new logistics facility. Following this, the integration activities of the WMS software for the warehouse focused on activating the part dedicated to the shipping of goods and closing(?) the real-time inventory with warehouse operations.
Achievements
Simpler and faster inventory management with WMS software... Goodbye paper!
The collaboration between Onit and Terratinta has led to positive results in terms of warehouse and inventory management at the logistics plant.
The Terratinta company is pleased with the speed of the software implementation, especially with the dedicated goods entry system, which has enabled immediate and complete management of the warehouse at the new plant.
An important advantage derived from the WMS software concerns the possibility to follow, in a simple and fast way, the whole stock management and goods placement: as of today, the operators active in Terratinta's warehouse are guided through the process of order preparation with all the necessary information available on the wireless terminal.
Finally, the use of WMS management software has enabled the reduction of inventory in the warehouse, since complete monitoring of stock and stock breaks takes place. Shipments have also seen optimization: fewer errors and fewer delays thanks to the guidance followed by the operators.
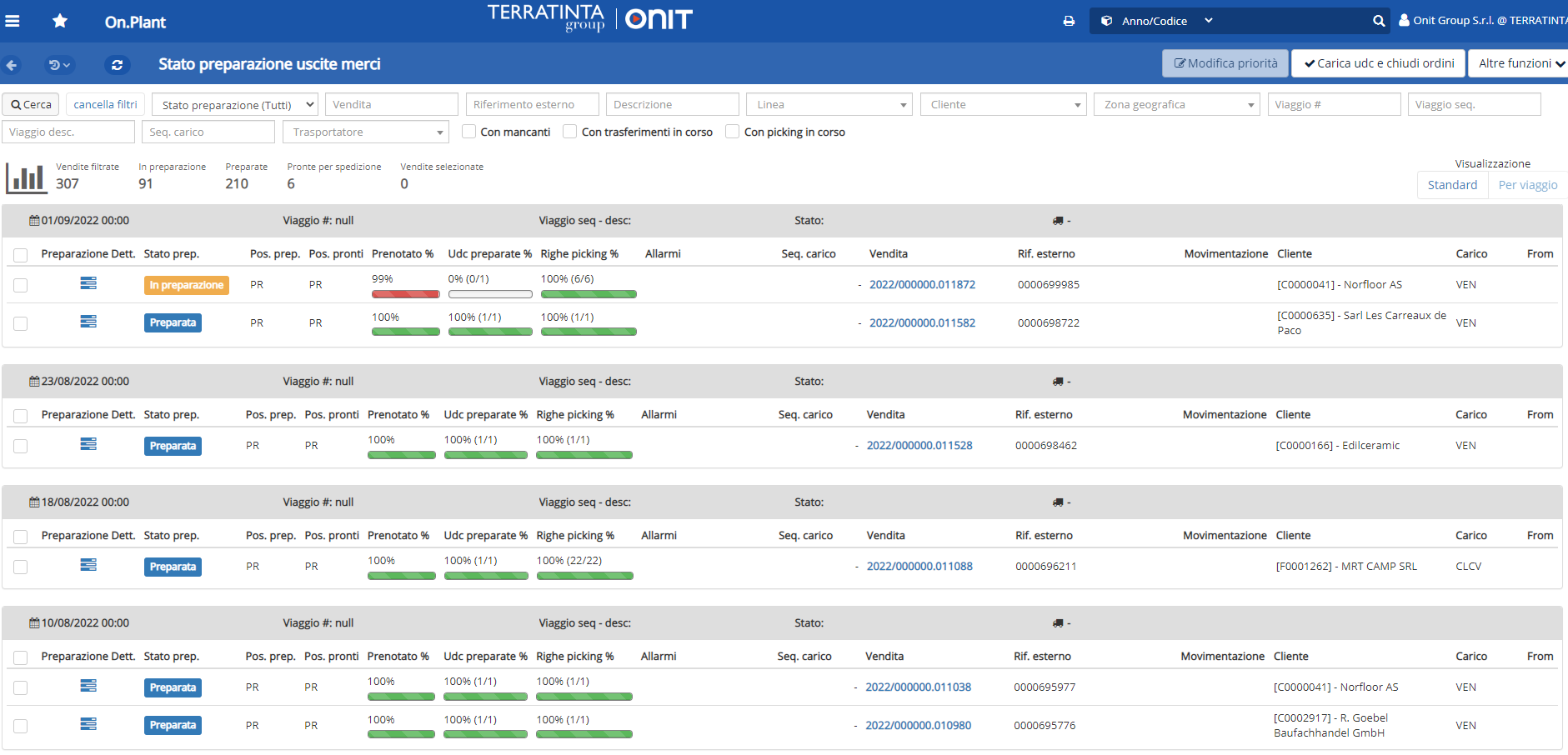