Asset Management System - AMS
Simplify the scheduling and monitoring of maintenance interventions to ensure the operation of company assets. Increase the responsiveness of maintenance technicians in the event of system failures, thanks to notifications sent to smartphones or PCs.
Description
AMS is Onit's software for Asset Management System, designed to enable strategic management of company asset maintenance processes and thus contribute to improving the value and competitiveness of companies.
Designed for use on the move, it allows you to easily plan maintenance interventions, anticipate possible critical situations and consult online all the documentation necessary to support maintenance technicians.
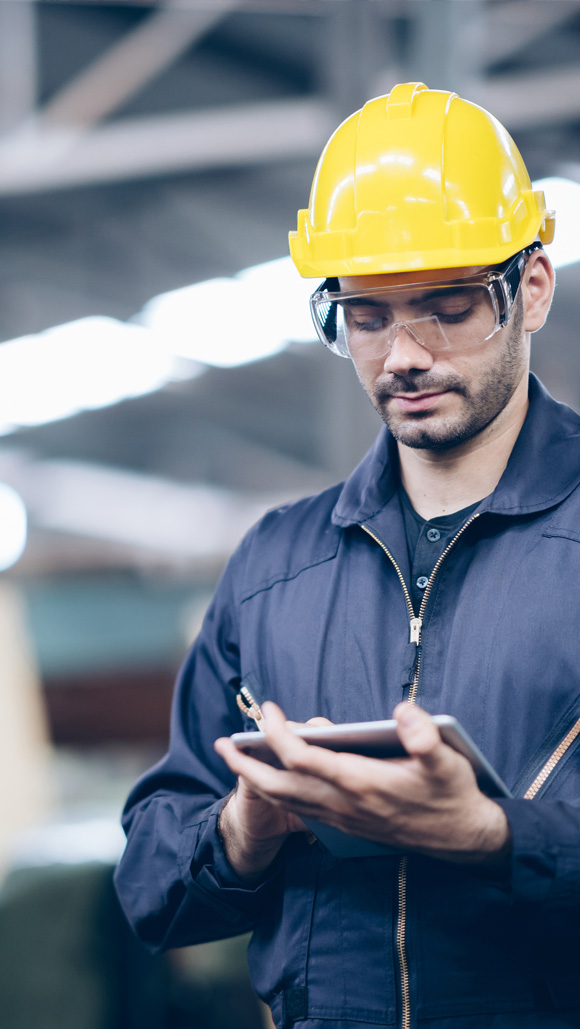
Advantages
- More reliability of company assets thanks to less downtime for breakdowns and maintenance
- Digitization and sharing of data relating to corporate assets
- Cost optimization thanks to preventive/predictive maintenance
- Simplification of the real-time management of interventions
- Better quality of maintenance interventions
- Increase in the commitment of maintenance workers in the management of interventions
AMS features that improve your work
Asset Management
The asset database contains all the information useful for management and operational purposes. The information elements of the asset are configurable and searchable by the user, in order to trace the type, location, use, etc. It is possible to attach documents such as certifications, manuals, technical data sheets, etc.
Classification hierarchies
It is possible to define multiple asset classifications, configuring hierarchies that can be viewed graphically via the navigation tree or directly on the factory layout, with asset sorting and drag & drop movement functionalities. In this way it is possible to analyze maintenance interventions by line/department/groups of assets, etc.
Spare parts management
The materials used in maintenance are registered, classified and associated with the reference assets. Complete management functions of the purchasing cycle are available (supplier price list, PO and Goods Receipt) possibly integrated with external warehouse management systems (e.g. ERP, WMS).
Maintenance management
For each maintenance technician it is possible to manage personal data, professional qualifications, role and certifications with relative deadlines. It is possible to configure groups of maintenance personnel with which to organize work teams.
Intervention workflow
Each intervention is based on a Work Order document (WOD), which is generated by a Request for Intervention (RI) upon notification (e.g. breakdown) or by a Maintenance Plan. The management workflow for the RI and the Work Order provides for the assignment to a manager, who will identify the maintenance technicians in charge.
Maintenance scheduling
Preventive maintenance plans represent templates of activities to be performed on assets or groups of assets. The plans are configurable on time frequencies (fixed or floating) or based on machine conditions/parameters. The system automatically generates the work orders based on the parameters set.
Mobile use
Fully usable via the web from any device, the system integrates with the smartphone/tablet camera to take photos that are automatically attached to the RI/Work Order. It also allows you to identify used assets and spare parts by reading the barcode/QR code on the identification labels.
IoT integration
It allows to acquire the machine parameters of the assets in real-time through an integration platform based on standard industrial protocols. The automatic data collection allows for the generation of maintenance interventions based on the conditions of the machine, also in predictive logic.
Alert system
The system manages notification events, both as system alerts and as e-mails, which are configurable for content, categories of events and recipients. The native integration with On.Plant/Automated Messaging Tool allows, if activated, the management of more complex alerting workflows.
Document management
All the technical documentation is filed and shared in the system, ensuring that all the information useful for the management of the intervention can be used. Certifications can also be managed by monitoring their expiration.